En esta planta se conjunta la habilidad humana con la más alta tecnología para producir uno de los vehículos icónicos de la marca, el Serie 3, de los cuales actualmente produce 35 vehículos por hora, aunque se planea que este número suba hasta 60 hacia el fin de año, para producir anualmente 175 mil automóviles.
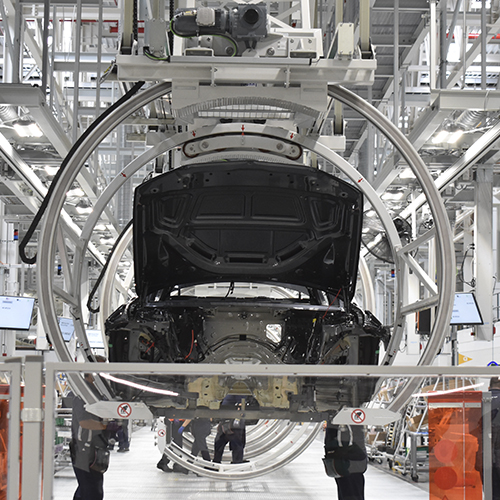
El proceso inicia en la nave de armado de carrocería, donde grandes robots sueldan las piezas que previamente acoplaron los especialistas humanos apoyados de otros robots.
Las carrocerías están armadas con una mezcla de materiales que incluye aluminio y le permite reducir hasta 55 kilogramos su peso, ofreciendo así, autos más ligeros con hechos con acero de alta resistencia y menos metal.
Su tecnología incluye remaches, pegamento y tornillos, que son unidos por medio de la colaboración entre humanos y robots.
De hecho, por cada robot que se utiliza, se generan empleos de alto nivel, de ahí que la planta cuenta con su propio centro de capacitación de aprendices, de donde han egresado cuatro generaciones.
En cada paso del armado del coche se observa la colaboración entre humanos y robots, y, es gracias a éstos últimos que las personas no cargan más de seis kilos en los procesos que realizan dentro de la planta productiva.
Durante el proceso hay incluso una estación de radar láser con cuatro unidades ópticas que lanzan un rayo láser a la carrocería y hacen mediciones.
Después del armado de la carrocería, los autos pasan a una línea de pintura que pasa por encima de la planta y crea un puente entre las naves, por donde los vehículos llegan a la nave de ensamble.
Todo el tiempo los vehículos son transportados en líneas de producción bien definidas que no interfieren una con otra y permiten que el armado de autos sea continuo.
Al llegar a la planta de ensamble, al auto le retiran las puertas, a las que se les ensamblan sus partes, mientras el coche pasa por las líneas donde se le instala el motor, las defensas, los faros, los espejos laterales, los asientos y recubrimientos interiores.
En cada estación por la que avanza el auto, hay al menos cuatro colaboradores de BMW quienes se encargan de ensamblar las piezas a la unidad.
Para el momento en que se instalarán los faros, el auto ya cuenta nuevamente con sus puertas y a partir de ahí se dirigirá a la instalación de llantas.
Una vez concluido este paso, el auto es encendido por primera vez y avanza hacia la zona de pruebas bajo techo.
Todos los autos son probados bajo techo y en la planta también hay un área en la que se realizan pruebas del auto al aire libre, pero está destinado a los vehículos de nuevo lanzamiento.
Grandes avances tecnológicos
La nueva planta de BMW Group es pionera en el campo del mantenimiento inteligente al contar, por primera vez, con el software Smart Maintenance Assistant que permite planificar de antemano el mantenimiento de los equipos en toda la planta y con ello aumentar la disponibilidad de estos.
Hermann Bohrer, director de la planta en México destacó que desde el principio se proyectaron las instalaciones para poder reaccionar rápida y flexiblemente ante futuras variantes de modelos y volúmenes de producción.
“En nuestra planta ultramoderna, utilizamos tecnologías innovadoras del sector de la Industria 4.0. Nuestra planta se caracteriza por nuevas soluciones de automatización y modernos sistemas de asistencia a la conducción”, dijo.
Las actividades de servicio se basan en datos del equipo actuales e inteligentemente preparados y ya no se guían por intervalos de mantenimiento predefinidos, todo ello, a través de dispositivos inteligentes como tabletas y teléfonos inteligentes, donde los empleados reciben toda la información relevante sobre el estado de los equipos-
“La colaboración entre el hombre y el robot es visible sobre todo en el pre-montaje del motor. Aquí colaboran directamente los robots y los empleados. Mientras que el robot tiene la fuerza para girar el transductor pesado, el empleado posee la sensibilidad para la precisión de ajuste del atornillado final”, resaltó.
Sustentables
Además, se trata de uno de los complejos más sustentables en el país, pues cuenta con 70 mil metros cuadrados de paneles solares, con lo que genera suficiente energía para alimentar las áreas de ensamble y logística, mientras que el área de pintura reutiliza más del 80% del agua que utiliza en sus procesos y no genera aguas residuales en absoluto, ya que el agua necesaria para el proceso de pintura se somete a un tratamiento y se reutiliza.