ZF Technologies es líder en el mercado de amortiguadores, con más del 50% de participación de mercado bajo la marca BOGE. En su planta de Guadalajara, en Jalisco, hacen dos partes de la suspensión del auto: amortiguador delantero (strut), y amortiguador trasero.
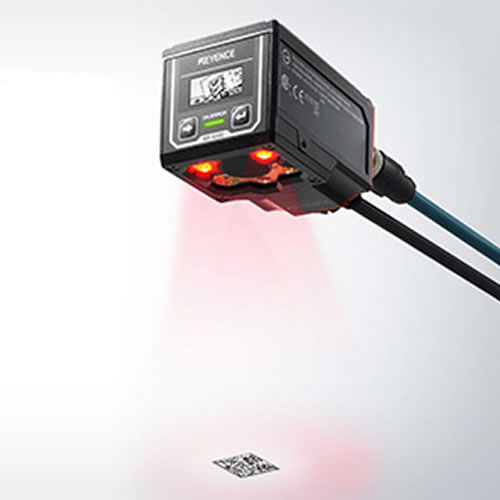
La célula de manufactura de ZF Technologies comprende diferentes estaciones. En cada una de ellas se suelda un componente a la pieza, y para finalizar el proceso de soldadura pasa por una cabina de inspección donde se corrobora que cuente con todos los componentes necesarios. Una vez aprobado este primer filtro, se le graba un Código Datamatrix por micropercusión, el cual es leído como paso final de la misma estación para verificar que sea legible e incluya los caracteres necesarios para que se pueda leer en otra parte del ensamble.
La adecuada aplicación de tecnología permite reducir paros no programados
En respuesta a esta necesidad, la empresa de origen alemán instaló una cámara que primero debía examinar cada pieza en busca de todos sus componentes, y posteriormente leer el Datamatrix para liberarlas o rechazarlas. Fue colocada a dos metros de la cabina de inspección, distancia necesaria para abarcar las dos partes del proceso, resultando en una solución no exitosa, ya que derivado de las múltiples dificultades para realizar la lectura tenían paros continuos.
“Metíamos piezas que no leía, entonces se acumulaban hasta que teníamos que parar para hacer una configuración nueva que además era muy complicada, porque implicaba hojas de cálculo y muchas fórmulas para llegar a las resoluciones”, explica Julio Gallegos, Ingeniero de Procesos en el área de soldadura, y responsable de la optimización de este procedimiento.
Esta problemática significaba que las piezas se liberaran con componentes faltantes, además de que existían dificultades para leer el Código Datamatrix. Fue así que decidieron cambiar a KEYENCE, cuyos asesores sugirieron emplear dos equipos para resolver sus retos. Con un sistema de procesamiento de
imágenes de ultra alta velocidad, XG-7502(P), hoy se asegura que la pieza cuente con todos los componentes, mientras que el lector de códigos, Serie SR-1000, permite validar el Datamatrix bajo cualquier condición.
De acuerdo con Gallegos, las herramientas de KEYENCE ayudaron a cambiar totalmente la manera de operar, pues ahora la configuración es mucho más sencilla y los ajustes más flexibles, lo que se traduce en velocidad total del procedimiento, “si yo configuro rápido, rápido voy a arrancar la línea. También es muy bueno en velocidad de lectura, porque reconoce las variables del Datamatrix muy rápidamente para poder liberar la pieza”, detalló.
Explicó que es un proceso complejo debido a que el Código Datamatrix no se graba sobre una superficie plana, sino que se trata de un tubo cóncavo que hace que el código sufra una deformación al momento de ser impreso, lo cual había sido difícil de leer con otras marcas; asimismo, al ser metálico existen retos de iluminación que se resuelven con la polarización automática del SR-1000.
Por otro lado, en materia de configuración se debía contemplar variables como altura, distancia, fijación, ambiente, deformación, profundidad, y ángulos, así como la necesidad de escanear diferentes diámetros de tubos, de manera que, por medio de los bancos de datos adecuados, el lector se ajusta automáticamente a las diferentes condiciones que implica el procedimiento (por ejemplo, alejamientos variables de los lentes).
Trazabilidad automatizada entrega certeza a los clientes
Posterior a la soldadura, la pieza se envía a la siguiente estación, donde la carcasa se recubre de pintura negra y una vez seca se manda al área de ensamble. Ahí se arma internamente con las demás piezas necesarias para el funcionamiento del amortiguador y cuando se finaliza se imprime una etiqueta, donde se asocia la información de trazabilidad de soldadura con la de ensamble.
Anteriormente se realizaba de forma manual, pero ahora ZF Technologies está implementando un proceso automatizado donde el mismo SR-1000 mande la señal de lectura a un archivo PDF y posteriormente se traduzca en una orden de impresión. “La principal ventaja es que se imprime al momento, además de que se elimina el lugar a error, pues anteriormente, cuando se imprimían etiquetas de diferentes códigos al mismo tiempo, existía la posibilidad de pegarlas incorrectamente, y teníamos que corroborar individualmente si correspondía la información del Datamatrix y la etiqueta”, indicó el directivo..
Con esta sincronización, se sabe con certeza el día, hora y turno en que se etiquetó, eliminando la necesidad de cotejar los datos manualmente, y teniendo un muestreo de lote optimizado. Considerando que cada línea de soldadura procesa diariamente alrededor de 3,000 piezas, durante seis días de la semana, la capacidad de rastrearlas eficientemente en caso de que se presente la necesidad, es algo de suma importancia.