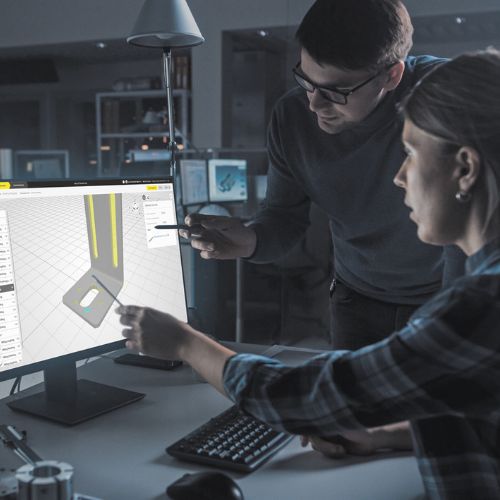
Además, el concepto de DFM está evolucionando debido a una cadena de suministro cada vez más globalizada y a una demanda creciente de productos personalizados. La movilidad eléctrica también afectará al DFM. Las piezas para vehículos eléctricos e híbridos varían más de un fabricante a otro que sus equivalentes para motores de combustión interna (ICE) y se fabrican cada vez más con materiales resistentes como aceros de baja aleación, Inconel y aluminio. Si bien las tendencias de movilidad eléctrica en el sector aeroespacial todavía están a años de imponerse, las tendencias en la industria automotriz ya están sobre nosotros: los fabricantes deben mantenerse al día con los cambios o arriesgarse a quedarse atrás.
¿Pero cómo pueden las soluciones de herramientas avanzadas marcar la diferencia para el DFM? Las respuestas se pueden encontrar en las fases de diseño asistido por computadora (CAD) para componentes de la fabricación. CAD para componentes puede referirse a tres etapas de fabricación. En primer lugar, la fase de CAD para husillos en la que se utilizan modelos CAD y de fabricación asistida por computadora (CAM), incluidas simulaciones similares a las de gemelos digitales, para preparar una operación de mecanizado y garantizar que las herramientas, la pieza de trabajo y los parámetros de mecanizado estén optimizados.
En segundo lugar, la etapa de husillos o las operaciones de mecanizado reales. Aquí, podemos evaluar el rendimiento de mecanizado de la herramienta en comparación
con la pieza de trabajo y su efecto en el costo por pieza, el costo por barreno y, en última instancia, en el balance final de nuestros clientes. En tercer lugar, está la fase de simple a componente donde se evalúa la calidad y el acabado del componente final. Ya sea para la ingeniería automotriz, aeroespacial o general, el acabado y características como la integridad de la superficie del barreno son de suma importancia. Una mejor calidad del barreno evita fallas en los componentes, y depende en gran medida de los procesos de fabricación que se utilizan para mecanizar o terminar los barrenos.
En particular, el diseño de una broca es fundamental para producir barrenos de mejor calidad. Esta es la razón por la que las geometrías de punta en brocas evolucionan continuamente, ya que es importante cumplir con los más altos estándares de fabricación y calidad de las piezas. El uso de refrigerante también es importante para reducir la acumulación de calor en la herramienta. Aquí es donde los especialistas de Sandvik Coromant pueden desempeñar un papel crucial para ayudar a sus clientes.
Fabricado con facilidad
Sandvik Coromant trabaja codo con codo con el cliente para recopilar toda la información relevante sobre su proyecto de mecanizado y ver qué es lo que se necesita.
Supongamos que el cliente necesita realizar una operación de perforación continua en una pieza de trabajo de acero inoxidable 316L, un material que, como se muestra en un estudio publicado por la Revista de Ingeniería y Ciencias Aplicadas de Asian Research Publishing Network (ARPN), se ha encontrado que experimenta un “desgaste rápido y fatal”, lo que afecta severamente la vida útil de las herramientas de corte.
En esta etapa del proceso de mecanizado del cliente, la etapa de CAD para husillos antes mencionada, nuestros especialistas pueden examinar y aplicar ingeniería inversa a los procesos del cliente, incluido el uso de modelos CAD y CAM. De esta forma, Sandvik Coromant puede desarrollar un prototipo de herramienta por la mañana y tenerla lista para probarla en R&D por la tarde. En la época previa a la era digital, este proceso habría requerido que los planos fueran y vinieran varias veces y habría tomado hasta seis semanas. Hoy en día, tener la capacidad de entregar prototipos de herramientas el mismo día ha sido un cambio radical para Sandvik Coromant.
Mayor vida útil de la herramienta
Sandvik Coromant ofrece una gama de productos para ayudar a sus clientes en la fabricación de componentes, incluidos los componentes para la movilidad eléctrica.
Esta gama incluye la CoroDrill® 860, una broca de carburo sólido diseñada para una perforación rápida y sin problemas que maximiza la productividad gracias a su alta eficacia de corte de metales. Esta herramienta está disponible en una variedad de geometrías, incluida 860 mm para materiales de acero inoxidable de viruta larga, como aceros inoxidables austeníticos, súper austeníticos, ferríticos y dúplex.
También está la CoroDrill® 860-GM que, para los fabricantes de automóviles, ha resultado útil para perforar bloques de motores, carcasas, bridas y colectores. Esta broca no solo es adecuada para las aplicaciones de la ingeniería automotriz y general, sino también para todas las aplicaciones en que la calidad del barreno es crítica, como en las industrias aeroespacial, del petróleo y gas, nuclear y de energía renovable.
La 860-GM ha logrado resultados impresionantes, incluso para un fabricante de automóviles en Corea. La operación de este cliente de Sandvik Coromant consistía en perforar barrenos en un lote de producción de conectores de transmisión para automóviles. El objetivo era perforar ocho barrenos pasantes de 8.2 mm (0.32”) de diámetro en cada componente, con una profundidad de 10 mm (0.39”). La solución existente produjo 200 componentes, 1600 barrenos en total, con una velocidad de corte (Vc) de 80 m/min (3102 RPM) y avance de corte (Vf) de 381 mm/min. En comparación, CoroDrill® 860-GM produjo 2300 componentes (18400 barrenos) con una Vc de 100 m/min (3878 RPM) y una Vf de 814 mm/min.
En general, CoroDrill® 860-GM brindó una mejora significativa del 1150% en la vida útil de la herramienta. Esto estuvo acompañado por un aumento de la productividad que ayudó a reducir significativamente el costo por pieza para el cliente. Otros clientes de Sandvik Coromant en el sector automotriz de todo el mundo han obtenido resultados igualmente impresionantes.
Tan importante como perforar barrenos lisos es el roscado, que es la acción que crea una rosca dentro del barreno. Para ello, Sandvik Coromant ofrece CoroTap® 100, 200, 300 y 400, cada una de estas herramientas optimizada para distintas aplicaciones. Para ver un par de ejemplos, CoroTap® 100 es una gama de roscas de acanalado recto optimizadas para materiales de viruta corta ISO K, ISO N e ISO H. También está CoroTap® 400, una rosca de conformado sin virutas de alta velocidad adecuada para barrenos ciegos y pasantes en acero, acero inoxidable y aluminio. La elección del cliente depende de lo que sea mejor para su aplicación.
En el futuro, Sandvik Coromant ofrecerá CoroTap® 100-N y CoroTap® 400-N. Cada una está diseñada para ayudar a los clientes con aplicaciones de roscado en aluminio, que se está volviendo más prominente en los procesos de fabricación.
Rendimiento
Por ahora, el rendimiento de las herramientas de corte de Sandvik Coromant muestra cómo las herramientas diseñadas para soportar el perforado y roscado de múltiples materiales serán vitales para ayudar a los fabricantes a producir componentes más ligeros, más pequeños y variados. Con nuestras soluciones, no solo pueden diseñar y desarrollar estas piezas de manera más fácil y rentable los talleres de mecanizado, sino que también pueden garantizar que el DFM siga siendo una prioridad durante todo su proceso de fabricación, y de esta forma innovar con eficiencia.